dunkelheit_phoenix_2008
Member
- Joined
- Dec 8, 2020
- Messages
- 70
- Points
- 8
This is a DC-DC stepdown circuit for laser control (better option than a LM311), at engineering level, it's based on texas instrument documentation, for testing proves I used three 9W 1Ohm resistors in parallel, the elementrical characteristics prove to work well with the laser load. There you have the electrical circuit:
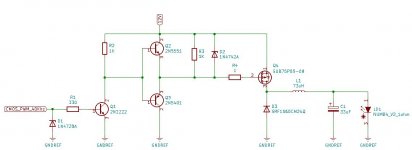
You'll find more information on:
Mechatronic Strike wordpress.
Hope this information was usefull, have a nice day.
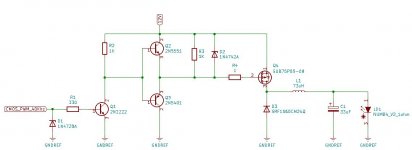
You'll find more information on:
Mechatronic Strike wordpress.
Hope this information was usefull, have a nice day.